Mit dem Dual Fluid Reaktor stellen die Mitglieder des Instituts für Festkörper-Kernphysik (IFK) Berlin ein neues inhärent sicheres Nuklearkonzept vor, das von Anfang an auf optimale zivile Nutzung ausgerichtet war. In der nun abgeschlossenen vierjährigen Konzeptionierungsphase wurden Materialien, Bearbeitungstechniken sowie vergangene Reaktorkonzepte insbesondere der sogenannten Generation IV auf den Prüfstand gestellt. Leitfaden war dabei nicht die inkrementelle Verbesserung vorhandener Systeme oder Konzepte, sondern ein kompletter Neuentwurf nach dem heutigen Stand der Technik und Wissenschaft mit dem Ziel einer Kostenoptimierung. Ausgangspunkt ist eine vor 2 Jahren eingereichte Patentschrift, die auf der Grundidee von zwei umlaufenden Flüssigkeiten, einer für den Brennstoff und einer für die Wärmeabfuhr, basiert. Durch den dadurch möglichen kompakten und integralen Kraftwerksbau ergeben sich Effizienzsteigerungen um einen Faktor 20 gegenüber heutigen Leichtwasserreaktoren. Der DFR wurde auf der IAEA-Konferenz FR13 (4.-7. März 2013 in Paris) erstmalig einem breiteren Fachpublikum vorgestellt. Das Konferenzproceeding kann hier heruntergeladen werden.
Erntefaktoren
Bei der Spaltung eines Atomkerns wird 100 Millionen mal so viel Energie freigesetzt wie bei der Verbrennung eines Kohlenstoffatoms. In Anbetracht dieses Verhältnisses ist es erschreckend, dass heutige Nukleartechnik nur 3-4 mal so effektiv Strom erzeugt wie Kohle- und Gaskraftwerke (siehe dazu auch die begutachtete Veröffentlichung zu Erntefaktoren, Preprint hier). Natürlich ist für die Nutzung eines Energieträgers mit derartig hoher Energiedichte auch ein höherer Aufwand erforderlich, insbesondere für die Förderung von Uran und Thorium verglichen mit Kohle, Gas und Öl. Die eigentliche Ursache dieses extremen Missverhältnisses liegt jedoch im militärischen Ursprung der Kerntechnik. Dort zur Perfektion entwickelt, verlieren viele Konzepte, allem voran die Verwendung fester Brennelemente, ihren Bezug, wenn sie auf zivile Anwendungen wie die großflächige Stromversorgung angewendet werden. Für das Militär steht eben die Wirtschaftlichkeit nicht im Vordergrund, sondern die Effektivität im Kriegseinsatz.
Generation IV
Der nukleare Brennstoffträger unterliegt in einem laufenden Reaktorkern ständigen Veränderungen wie Abbrand und Anhäufung von Spaltprodukten. Die angemessene technische Antwort wäre demnach eine kontinuierliche Aufarbeitung, was nur durch einen zirkulierenden flüssigen Brennstoff kostengünstig machbar ist. Die Verwendung fester Brennelemente für zivile Anwendungen war von Anfang an eine Entwicklung, die auf die militärische Festlegung zurückzuführen ist, deren Weiterentwicklung aber heute nicht mehr zu rechtfertigen ist. Auch die vom Generation-IV-Forum festgesetzten Reaktorkonzepte, die frühestens ab 2030 in Betrieb gehen sollen, sind nichts anderes als lange in der Vergangenheit entwickelte Typen mit militärischem Hintergrund. Dies erklärt, warum 5 der 6 Konzepte wiederum feste Brennelemente enthalten. Siehe dazu auch nebenstehende Abbildung.
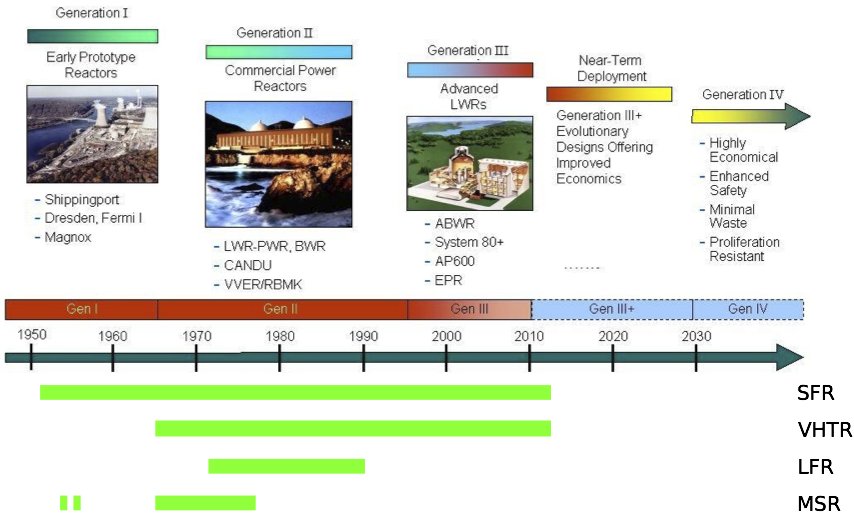
Flüssigsalzreaktoren
Flüssiger nuklearer Brennstoff kann z.B. in metallischer Form vorliegen, in der historischen Entwicklung hatte sich aber zunächst die Verbindung von Aktiniden mit Fluor oder Chlor zu Salzen, die bei einigen Hundert °C flüssig werden, als die günstigere Variante bewährt. Schon in den 1960er Jahren lief am Oak Ridge National Laboratory das „Molten Salt Reactor (MSR) Experiment”, MSRE. Es wurde erfolgreich abgeschlossen, musste aber der Entwicklung von metallgekühlten Reaktoren weichen. Zwar wurden letztere dann in den USA auch nicht konsequent umgesetzt, aber die Entwicklung von Flüssigsalzreaktoren kam dadurch zum Erliegen. Außerdem waren Leichtwasserreaktoren mit Brennstäben bereits wirtschaftlich. In letzter Zeit ist das MSRE-Konzept wiederentdeckt worden, wie z.B. im WAMSR von Transatomic Power, und im MSR-Konzept der Generation IV, allerdings sind hier bis auf den Übergang zu Schnellspaltreaktoren keine grundsätzlich neuen Entwicklungen zu verzeichnen. Dies gilt auch für das beschleunigergetriebene System GEM*STAR der amerikanischen ADNA Corporation.
Beim MSRE wurde das Hauptaugenmerk auf einen flüssigen homogenen Reaktorkern gelegt, ohne dass die dadurch entstehenden Nachteile Beachtung fanden. Das Flüssigsalz sollte dabei auch gleichzeitig die Wärme abführen. Was zunächst eine Vereinfachung darstellte führte jedoch zur weitgehenden Aufhebung der Vorteile von Flüssigsalzen, welche nun extrem schnell zirkulieren mussten, um die Nutzwärme abführen zu können. Und damit nicht genug, der eigentliche Brennstoff musste extrem verdünnt werden, um nicht zu viel Wärme zu produzieren. Durch die schnelle Zirkulation konnte das Flüssigsalz nicht bei laufendem Reaktor aufgearbeitet werden. Außerdem war durch die Verdünnung die Aufarbeitung sehr aufwendig und die Leistungsdichte stark beschränkt, was den Konstruktionsaufwand erheblich vergrößerte und die energetische und damit wirtschaftliche Effizienz stark reduzierte. Dies hat sich in den neueren MSR-Konzepten grundsätzlich nicht verbessert.
Das Dual-Fluid-Prinzip

Im Konzept des Dual Fluid Reaktors, DFR, wird dieses Manko nun korrigiert, indem die beiden Funktionen Brennstoff und Wärmeabfuhr getrennt werden. Auch wenn die Gesamtanordnung dadurch zunächst komplizierter wird, ergeben sich erhebliche Vereinfachungen an anderen Stellen sowie Synergien, die zu einer enormen Effizienzsteigerung führen. Mit dem Wegfall der Doppelfunktion des Salzes kann man sich nun ganz auf die Ausnutzung der Vorteile einer Online-Aufbereitung eines unverdünnten Brennstoffflüssigkeit einerseits, sowie einer effektiven Wärmeabfuhr andererseits konzentrieren. Für letzteres eignen sich besonders Flüssigmetalle.
Zwei Flüssigkeiten
Die Verwendung von salzförmigen Spaltmaterialien als Brennstoff ist übrigens nicht zentraler Bestandteil des DFR-Patents, entscheidend ist vielmehr, dass im Reaktorkern allgemein zwei Flüssigkeiten laufen, wovon eine den Brennstoff bereitstellt und die andere die Nutzwärme abführt (Kühlmittel). Insofern ist der DFR nicht automatisch ein Flüssigsalzreaktor, im Gegenteil, eine Brennstoffzufuhr in Form von Flüssigmetallen würde die Effizienz nochmals erheblich steigern und an die Grenze des Potentials der Kernspaltung führen. Als erster Entwicklungsschritt des DFR, insbesondere in Hinsicht auf die Online-Aufbereitung, ist die Verwendung von Flüssigsalzen jedoch zunächst die bevorzugte Variante. Dadurch vereinfacht sich der Entwicklungsaufwand, und ein kommerzielles Kraftwerk kann früher realisiert werden.

Blei zur Wärmeabfuhr
Zur Wärmeabfuhr eignet sich Blei besonders gut. Es wird kaum durch den hohen Neutronenfluss aktiviert und kann ohne Zwischenkreislauf direkt in den konventionellen Teil geleitet werden, wo sich der Wärmetauscher befindet. Die Arbeitstemperatur beträgt 1000 °C, was eine effektive Stromproduktion ermöglicht. Bei diesen Temperaturen öffnet sich auch die gesamte Kette der Prozesschemie, da nun die wettbewerbsfähige Produktion von Wasserstoff möglich wird. Damit können auch sehr kostengünstig synthetische Kraftstoffe als Benzinersatz hergestellt werden.
Die Aufbereitung findet im Containment des Reaktors im automatischen Betrieb statt. Bevorzugt sind hier Methoden der fraktionierten Destillation und Rektifikation, wie sie in der Großindustrie täglich zum Einsatz kommen. Für das Flüssigsalz des DFRs genügt allerdings eine Kleinanlage, die „Pyrochemical Processing Unit”, PPU, die direkt in den Kreislauf des Flüssigsalzes mit dem Reaktorkern verbunden ist. Dort erfolgt die Auftrennung nach Siedepunkten, was sehr hoher Temperaturen (bis zu 2000 °C) bedarf, wobei die Restzerfallswärme der hochradioaktiven Spaltprodukte hierbei sogar unterstützend wirkt (im nächsten Abschnitt wird auf die Abfuhr der Restzerfallswärme unter dem Aspekt der Sicherheit allgemein eingegangen). Die Bearbeitung findet selbstverständlich gekapselt und im wesentlichen automatisch statt, was erheblich höhere Aktivitäten als z.B. beim PUREX-Verfahren erlaubt. Eine hohe Aktivität und damit Zerfallswärmeleistung ist bei den hohen Temperaturen sogar hilfreich.
Sicherheitsaspekte beim DFR
Bei einem Kernkraftwerk muss in allen Betriebszuständen, insbesondere während des Betriebs und der Kühlphase nach Abschaltung, der sichere Einschluss von radioaktivem Inventar gewährleistet sein. Bei heutigen Leichtwasserreaktoren sind lediglich die Kapselungen bzw. Umbauten (Containment) sowie das Installieren von Wasserreservoiren als Wärmespeicher die einzigen passiven Sicherheitselemente. Alle anderen Systeme sind aktiv und können technisch bedingt versagen. Durch ihre redundante wie diversitäre Auslegung erreicht man dennoch eine hohe Sicherheit, allerdings zu hohen Kosten, was durch die Hochdruckumgebung noch verstärkt wird.
Drucklose Flüssigkeiten
Das DFR-Konzept nutzt hier alle Vorteile praktisch druckloser Flüssigkeiten, wobei die Brennstoffflüssigkeit (Salz) kaum Wärmetransportaufgaben hat. Neben Mehrfachcontainments, die auf niedrigen Druck auslegbar und damit kostengünstig sind, können Flüssigkerne wesentlich einfacher als feste Kerne separiert und bearbeitet werden. Nachzerfallswärmekomponenten können so problemlos nach Wärmeleistung aufgeteilt werden. Daher befinden sich im DFR-Kern überwiegend kurzlebige Spaltprodukte (Halbwertszeiten bis zu einigen Stunden, d.h. hohe Wärmeleistung), und in einem weiteren Zwischenlagerbehälter (ebenfalls im Bleikreislauf, s. Abbildung „DFR-Reaktorkern”) solche mit Halbwertszeiten von bis zu einigen Monaten. Im eigentlichen Spaltproduktelager (Zwischenlager, s. Abb. „Kraftwerk…”) außerhalb des Bleikreislaufs liegen zumeist Stoffe mit Halbwertszeiten von Jahren bis Jahrzehnten.
Aktiv gekühlte Schmelzsicherung
Kern und Behälter im Blei sind an einer aktiv gekühlten Schmelzsicherung angeschlossen. Wenn nun der gesamte Strom ausfällt, wird die Nachzerfallswärme problemlos durch das Blei ausschießlich über Naturkonvektion abgeführt. Kann auch das Blei seine Wärme nicht mehr abgeben (Ausfall aller Sekundärkreisläufe), so wird dieses und damit das Salz heiß und die Schmelzsicherung wird durchlässig. Beide Salzreservoire fließen dann in tiefergelegene Tanks, die von gut leitendem Material hoher volumetrischer Wärmekapazität (z.B. Eisen) umgeben sind, welches die Zerfallswärme für mehrere Wochen aufnehmen und dann passiv an die Umgebung abgeben kann. In jedem Fall ist keine aktive Sicherung, die versagen könnte, vorhanden.
Passive Sicherungssysteme
Auch im Betrieb wirken vor allem passive Sicherungssysteme. Leckagen sind sicherheitstechnisch eher unproblematisch: Sowohl in Blei eintretendes Sekundärkühlmittel (hier Wasser) als auch das Blei selbst können wegen ihrer geringen Aktivität keinen radiologischen Schaden anrichten. Wegen der hohen Bleimasse wäre der Eintritt auch bei hohem Druck nicht schlagartig. Blei erstarrt bei Austritt in den konventionellen Bereich schnell. Wegen des, im Vergleich zu Reaktoren mit festen Kernen, sehr stark negativen Reaktivitätskoeffizienten kann keine Leistungsexkursion erfolgen. Designbedingt nimmt der flüssige Kern außerhalb des Kernbereichs (auch im Blei wegen des Dichteunterschieds) immer einen unterkritischen Zustand ein, sollte der äußerst seltene Fall eines Lecks im Kern auftreten. In diesem Fall muss nur die aktive Kühlung der Schmelzsicherung abgeschaltet werden.
Bei natriumgekühlten Reaktoren wird ein Großteil der Sicherheitstechnik und damit der Kosten auf die Beherrschung bzw. Vermeidung eines Natriumbrandes verwendet. Dieses Problem entfällt durch die Bleikühlung beim DFR völlig.
Gute Neutronenökonomie und ihre Folgen
Im DFR behalten die Neutronen wegen der vielen massereichen Atomkerne (Aktinide und Blei) ihre hohe Energie. Blei selbst absorbiert ohnehin wenig Neutronen, und die Neutronenverluste in den Strukturmaterialien sind bei diesen Energien sehr gering. Auf der anderen Seite werden durch die schnellen Neutronen aber besonders viele davon nachgebildet, nämlich durchschnittlich 3 oder mehr pro Spaltvorgang. Bei fast allen Reaktoren ist das weniger, bei Leichtwasserreaktoren deutlich weniger. Diese Neutronen werden nun unterschiedlich „verbraucht”.
Eines der 3 Neutronen wird zur Aufrechterhaltung der nuklearen Kettenreaktion benötigt, ein weiteres, um den eigenen Spaltstoff nachzubrüten. Da die Verluste gering sind (weniger als 0,5 Neutronen durch unerwünschte Einfänge), bleiben noch mindestens 0,5 Neutronen pro Spaltung für andere Anwendungen übrig, mehr als bei allen anderen Reaktoren. Mit diesem hohen Überschuss kann man nun in erheblich kürzeren Zeiträumen als bei anderen „schnellen Brütern”, z.B. Plutonium (hier nicht waffenfähig), erbrüten und damit zügig die nächste Generation von Reaktoren installieren. Auch der Thorium-Uran-Prozess mit seiner kernphysikalisch bedingt niedrigeren Neutronenausbeute ist aufgrund der sehr guten Neutronenökonomie des DFR im Vergleich zu anderen Schnellspaltreaktoren besonders gut handhabbar. Alternativ können auch sehr effektiv problematische langlebige Spaltprodukte z.B. aus heutigen Reaktoren transmutiert und damit abgebaut werden. Sehr effizient ist aber auch die Bildung erwünschter Radioisotope, etwa für die Medizin. Die PPU erfüllt hier eine wichtige Aufgabe, die ständige chemische Trennung von Stoffen untereinander und vom Brennstoff, was auch die Minimierung von „Neutronenfängern”, sogenannten Neutronengiften und damit auch die Neutronenverluste reduziert.
Letzteres ist übrigens auch für die Leistungsregelung des DFR sehr günstig. Wegen des permanent immer sehr „sauberen” Reaktorkerns muss man keine Spaltstoffreserven einbringen, die über ein kompliziertes Regelsystem (Steuerstäbe) während ihres Abbrandes ausgeglichen werden müssten, wie etwa in heute gängigen Leichtwasserreaktoren. Dies begünstigt auch einen sogenannten unterkritischen Betrieb, bei dem fehlende Neutronen durch ein Beschleunigersystem nachgeliefert werden („Accelerator Driven Subcritical System”, ADS). Je näher man sich stabil der Kritikalität nähern kann, desto kleiner darf der Beschleuniger sein. Beim DFR könnte der Beschleuniger nun auf eine Länge von wenigen Metern reduziert werden, im Vergleich z.B. mit dem belgischen ADS-Projekt „MYRRHA”, welches einen mehrere 100 Meter langen Beschleuniger benötigt.
Zudem reagiert ein flüssiger Reaktorkern auf eine Temperaturerhöhung sehr schnell mit Ausdehnungen, genauso auch das Blei, was diesen außen umgibt. Die Abstände der Atomkerne werden bei Temperaturerhöhung größer, wodurch gleich zwei Wahrscheinlichkeiten sinken, zum einen, dass ein Neutron im Flüssigsalz eine Spaltung induziert, zum anderen, dass es am Blei reflektiert wird. Somit fällt die Leistung mit einer Temperaturzunahme sehr schnell ab. Dieser negative “Temperaturkoeffizient” ist durch das Dual-Fluid-Prinzip so stark ausgeprägt, dass bereits innerhalb eines Temperaturanstiegs von wenigen 10 Kelvin die Leistung eingestellt werden kann. Die Spaltrate folgt somit zügig der Leistungsentnahme, welche wiederum durch die Geschwindigkeit der Bleizirkulation eingestellt werden kann. Da dieser Mechanismus ohne technisches Eingreifen aufgrund physikalischer Gesetze immer funktioniert, kann der Reaktor auch nicht durch einen unkontrollierten Leistungsanstieg “durchgehen” – er ist in diesem Punkt inhärent sicher.
Blei und Salz bei 1000 °C
Materialien, die den Bedingungen im Reaktorkern (Blei, Salz, 1000 °C, Neutronenfluss) standhalten können sind seit Jahrzehnten bekannt. Dazu gehören insbesondere Legierungen aus der erweiterten Gruppe der Refraktärmetalle. Diese überaus widerstandsfähigen Legierungen konnten in der Vergangenheit nicht hinreichend verarbeitet werden. Mittlerweile ist die Fertigungstechnik jedoch so weit vorangeschritten, dass derartige Legierungen in allen Bereichen der Industrie, insbesondere der chemischen Industrie, im Maschinenbau und auch in der Luftfahrt immer mehr Anwendungen finden. Als weitere Option kommen neue Keramiken als Beschichtungen oder in Form neuartiger faserverstärkter Komposit-Werkstücke hinzu. Mikrokristalline Schäden durch den hohen Neutronenfluss sowie thermischer Stress werden bei der hohen Temperatur automatisch ausgeheilt (Ausglüheffekt). In der PPU gibt es sogar noch weniger Einschränkungen, da Neutronenversprödung und Wärmeleitung hier keine Rolle mehr spielen.

Hochleistungslegierungen, auch refraktäre, können durch neue Elektronenstrahlschweißverfahren, Hochdichtsinter- und Lasertechniken hergestellt werden. Gerade die Laserbehandlung sorgt hier für eine hochreine Kristallgitterstruktur (Glattschmelzen), ein für die Korrosionsbeständigkeit wichtiger Faktor. Für Ventile im Flüssigsalz können Kontaktflächendichtungen verwendet werden, sie werden nur etwa stündlich betätigt. Die immer noch hohen Kosten spielen beim DFR eine untergeordnete Rolle, da der Materialbedarf deutlich geringer als bei Leichtwasserreaktoren ist (mehr zu den Materialien hier). Insgesamt müssen bekannte, neue Fertigungsprozesse, die dann auch eine Wartung erlauben würden, etabliert werden. Heute werden sie wegen mangelnder Nachfrage selten genutzt, ihre technische Machbarkeit wurde jedoch in den letzten Jahrzehnten bewiesen. Die Standfestigkeit ist hier ein zentraler Punkt, denn die nuklearen Aspekte im DFR erlauben es ja gerade, den Kern nicht tauschen zu müssen. Dieser Punkt wird von Kritikern oft verkannt, die implizit von der bei festen Brennelementen üblichen „Wegwerftechnik” ausgehen, und somit eine sehr eingeschränkte Sicht auf die Materialvielfalt entwickelt haben.
Da beim flüssigen Brennstoffsalz eine ständige Aufbereitung möglich ist, sammeln sich wenig Spaltprodukte an, somit ist deren Aufnahme im Salz unproblematisch. Die niedrige Spaltstoffkonzentration im Kern vermindert dort die Korrosion, flüchtiges Jod und Cäsium können in der PPU abgezogen und chemisch stabil gebunden werden. Das Salz muss für den Betrieb flüssig bleiben, was im Kern durch die Kritikalitätsbedingungen und in der PPU durch die Nachzerfallswärme gegeben ist. Sicherheitstechnisch ist ein Erstarren des Salzes unproblematisch, es muss dann nur (z.B. induktiv) vorgeheizt werden.
Verspannungen?
Die hohen Betriebstemperaturen liegen im Duktilbereich von Refraktärmetallen, was eine Versprödung stark hemmt. Zudem können im Kern auch noch hochbeständige Beschichtungen in Betracht gezogen werden. Diverse Refraktärlegierungen sind bereits zwischen 300 °C und 500 °C (oder niedriger) duktil, z.B. MHC (Molybdän-Hafnium-Carbon mit 98 Massenprozent Molybdän) oder TZM (Titan-Zirkon-Molybdän mit 99 Massenprozent Molybdän), ggf. mit Zugaben von Rhenium im 1%-Bereich. Die Betriebstemperatur (Eintritts- wie Austrittstemperaturen) liegt immer zwischen 850 °C und 1100 °C. Sobald das Salz (auf mindestens °900 C vorgeheizt) langsam in den Kernbereich eingelassen wurde, wird es kritisch. Durch den sehr stark negativen Reaktivitätskoeffizienten pendelt sich sofort eine Gleichgewichtstemperatur ein, und es kann nicht mehr erstarren (Schmelztemperatur um 800 °C). Die Längenausdehnung von Refraktärlegierungen entspricht denen von Keramiken, hier gibt es keine Verspannungen.
Fertigung
Der gesamte Kern (Leergewicht um 15 bis 25 Tonnen) kann in einer Fabrik gefertigt und an Ort und Stelle ausschließlich mit Schraubverbindungen verbaut werden. Die genannten Fertigungstechniken (inklusive evtl. Beschichtung) kommen nur in der Fabrik zum Einsatz. Eventuell wird der Kern geeignet segmentiert, um einzelne, defekte Rohre leichter auszutauschen. Da im gesamten Reaktor nur wenige 100 Tonnen refraktäre Materialien (davon 80 bis 90% einfache Geometrie) zum Einsatz kommen, darf hier der Aufwand hoch sein, auf die Gesamtkosten wirkt sich das nicht nennenswert aus. Bei den Beschichtungen gibt es korrosionsfeste Materialien (SiC, Titandiborid,…), die eine dem Nickel ähnliche Wärmeleitfähigkeit haben. Als Isolierung können Fächer-, Faltbleche usw. verwendet und der Kern muss wegen des hohen Neutronenflusses sowieso zusätzlich in Beton verpackt werden.
Der konventionelle Teil: Erweiterte Möglichkeiten
Das längerfristige Ziel ist die Entwicklung eines Direktwärmetauschers von Blei zu Gas, sowie die direktere Wandlung in Elektrizität über MHD-Generatoren, wie auch in der Patentschrift beschrieben. Für die zügige Umsetzung ist hingegen die Verwendung von superkritischem Wasser, wie es bereits in 500 Kohlekraftwerken zum Einsatz kommt, vorgesehen. Dies ist das Referenzkraftwerk, wie es auch in den Skizzen und Videos zum DFR gezeigt ist.
Anders als im Reaktorkern können beim Wärmetauscher zu Wasser oder Gas auch mit Oxiden verstärkte Refraktärbasislegierungen (z.B. Molybdän mit Zugaben etwa von Cer- bzw. Yttriumoxid und/oder Silizium bzw. Bor im Prozentbereich) verwendet werden. Diese zeichnen sich bei guter Warmfestigkeit durch eine sehr gute Bearbeitbarkeit, Dehnbarkeit und Duktilität bei niedrigen Temperaturen aus, was die Rissgefahr deutlich reduziert. Ihre deutlich erhöhte Oxidationsbeständigkeit sorgt bei einem Riss in der schützenden Beschichtung noch für viele Stunden Betrieb, ehe diese Stelle gewartet werden muss.
Im Falle eines Lecks verläuft eine Reaktion von Blei mit Wasser selbst bei diesen Temperaturen sehr langsam, zudem ist das Blei auch nach langer Betriebszeit kaum radioaktiv (etwa wie Natururan, Halbwertszeit 3h). Die mitlaufende Überwachung der Neutronenflussdichteverteilung des Reaktors zeigt Veränderungen sehr schnell und präzise an; was gewissermaßen eine on-line Neutronentomographie ist. Die nun veränderte Bleikorrosion bekommt man mit Zusätzen (sogenannten Gettern oder Inhibitoren) in den Griff. Selbst in bleigekühlten U-Boot-Reaktoren, obgleich mit anderen Betriebsparametern, gab es solche Probleme aber nicht.
Die Eigenschaften des DFRs insbesondere des Flüssigmetallkühlmittels mit seiner hohen Wärmetransportfähigkeit ermöglichen mehrere neue Entwicklungsrichtungen im konventionellen Teil, die insofern interessant sind, da die Kosten für Turbinen und Generatoren dominierend sind aufgrund ihres komplexen mechanischen Aufbaus wegen der rotierenden Komponenten. Schon für die Generation IV Kraftwerke werden daher direktere Wandler anvisiert, wie MHD-Generatoren für flüssigmetall- und flüssigsalzgekühlte Reaktoren. Da MHD-Generatoren keine beweglichen Teile habe, sind sie günstiger als Turbinen. Andererseits ist ihr Wirkungsgrad begrenzt und die Restwärme sollte immer noch in einer Wasserdampfturbine genutzt werden, die allerdings viel kleiner ist als in einem System nur mit Turbinen. Eine weitere Möglichkeit, für die die Betriebsparameter des DFRs sehr gut passen, sind AMTECs (Alkali-metal thermal to electric converter / Alkalimetall thermisch zu elektrisch Konverter), die thermische Energie direkt in elektrische umwandeln können ohne den Zwischenschritt der Umwandlung in mechanische Energie und somit im Konverter auf bewegliche Teile ebenfalls verzichten können.
Was soll der Spaß kosten?
Vom IFK wurde eine grobe Kostenschätzung für ein Serienkraftwerk für ein 500-MW- als auch für ein 1.500-MW-Kraftwerk (elektrisch) erstellt, siehe auch hier. Trotz des hohen Bearbeitungsaufwand bewegen sich die Gesamtkosten für den Reaktorkern plus Primärkreislauf plus PPU im Bereich von 250 Mio. € (für 1.500-MW), was nur etwa 20% der Gesamtkosten ausmacht, die von den Turbinen dominiert werden. Bezogen auf die installierte Leistung ergeben sich dann Kosten von 1 €/Watt, deutlich unter denen eines modernen Kohlekraftwerks. Eine Test- und Demonstrationsanlage wird im nuklearen Teil sicher ein Vielfaches davon kosten, dafür muss der konventionelle Teil nicht vollständig aufgebaut werden.
Die Betriebskosten von gut 40 Mio. €/Jahr werden zu 50% von der Wartung für den konventionellen Teil dominiert, während die Brennstoffkosten durch die vollständige Nutzung praktisch keine Rolle mehr spielen. Weitere Kosten kommen nicht hinzu, denn Anreicherung, Aufbereitung sowie Entsorgung durch externe Anlagen entfallen. Dies führt in der Summe zu Stromgestehungskosten (Overnight, d.h. ohne Zinsen) von 0,6 ct/kWh. Entsprechend würde die prozesschemische Herstellung von synthetischen Kraftstoffen mit dem DFR etwa 10 (Ammoniak) bis 20 (Hydrazin) Cent je kg kosten, was auf den Energiegehalt von Mineralölkraftstoffen umgerechnet, 20 bis 40 Cent je Liter entsprechen würde.
Das Dual-Fluid-Prinzip ermöglicht durch die Autoregulation und die rein passive Restzerfallswärmeabfuhr die Vereinbarkeit von inhärenter Sicherheit und hoher Leistungsdichte, was für eine gute Wirtschaftlichkeit unabdingbar ist.
Fazit

Bei der beabsichtigten Implementierung neuer Techniken stellt sich zuvorderst die Frage, ob es offene Fragestellungen oder gar Unmöglichkeiten gibt, die in grundlegenden Gesetzmäßigkeiten der Natur liegen, so wie wir sie heute kennen. Wenn dies zutrifft, handelt es sich um Grundlagenforschung, wie bei alternativen Wegen zur kontrollierten Kernfusion (d.h. nicht ITER) oder der Energiegewinnung durch Umwandlung von Hadronen in Leptonen mit 99,9% Umwandlung von Masse in Energie (vorstellbares Ergebnis der Forschung am LHC des CERN). Trifft dies nicht zu, handelt es sich nicht mehr um Forschung sondern um ein technisches Entwicklungsprojekt. Auch im Laufe dessen werden unvorhergesehene Probleme auftauchen, die man dann löst, häufig verbunden mit einem Mehraufwand an Zeit und Kosten, was in der heutigen Zeit als willkommener Anlass genommen wird, eine neue Technik zu beerdigen, oder erst gar nicht zu entwickeln („Man weiß ja gar nicht ob das funktioniert!”). Aber auch im schlimmsten Fall einer objektiv technisch unüberwindbaren Hürde, wurden Erkenntnisse und Fertigkeiten gewonnen, die woanders eingesetzt oder später aufgegriffen einen Mehrwert schaffen. Dies alles wussten unsere Vorfahren noch; nur dadurch wurde der Aufbruch des 19. und 20. Jahrhunderts möglich. So bewertet ist der DFR ein rein technisches Entwicklungsprojekt.
Da die in einer Volkswirtschaft verwendete Energietechnik der Beginn und Multiplikator der industriellen Produktionskette ist, bestimmt ihre Effizienz die Produktivität der gesamten Kette. Von der Produktivität der Industrie wird direkt das Wohlstandsniveau bestimmt. Wird wie jetzt in Deutschland die Energieversorgung auf Techniken wie Wind, Sonne und Biomasse umgestellt, die nur ein Zehntel der Effizienz der fossilen Kraftwerke haben, bedeutet das eine Reduktion des Lebensstandards auf ein Zehntel, also das Niveau des Mittelalters. Der DFR ist in der Lage, die Effizienz der Kernenergie um mindestens eine Größenordnung zu steigern und damit die fossilen Kraftwerke um zwei Größenordnungen zu übertreffen. Dies schafft die notwendige Voraussetzung für die Steigerung des Wohlstandsniveaus um den gleichen Faktor. Nur wenn die Kernenergie der Gesellschaft einen offensichtlichen Vorteil bietet, kann sie sich durchsetzen. Dass sie das bisher nicht oder zu wenig bietet, ist der eigentliche Grund des schleppenden Ausbaus seit den 70er Jahren.
Götz Ruprecht, IFK
(Das IFK ist ein unabhängiges Forschungsinstitut, das weder private noch öffentliche Unterstützung erhält.)